Mould Welding Machine comes advanced in the world market and allows users to repair large moulds and tools with high level of quality. The cost of repairing the mould will always be cheaper than replacing it. The problem is the performance of refurbished mould in the future. Will it produce parts of equal quality to the original? How long will it last before it needs to be repaired again or needs to be discarded? The most common practice for rebuilding worn cavity surfaces is with TIG (tungsten inert gas) welding. However, plastics, Aluminum and zamak processors have found that the alternative, Mould Welding Machine, provides a superior result with less damage to the base material, so the mould produces better quality parts and the mould lasts significantly longer.
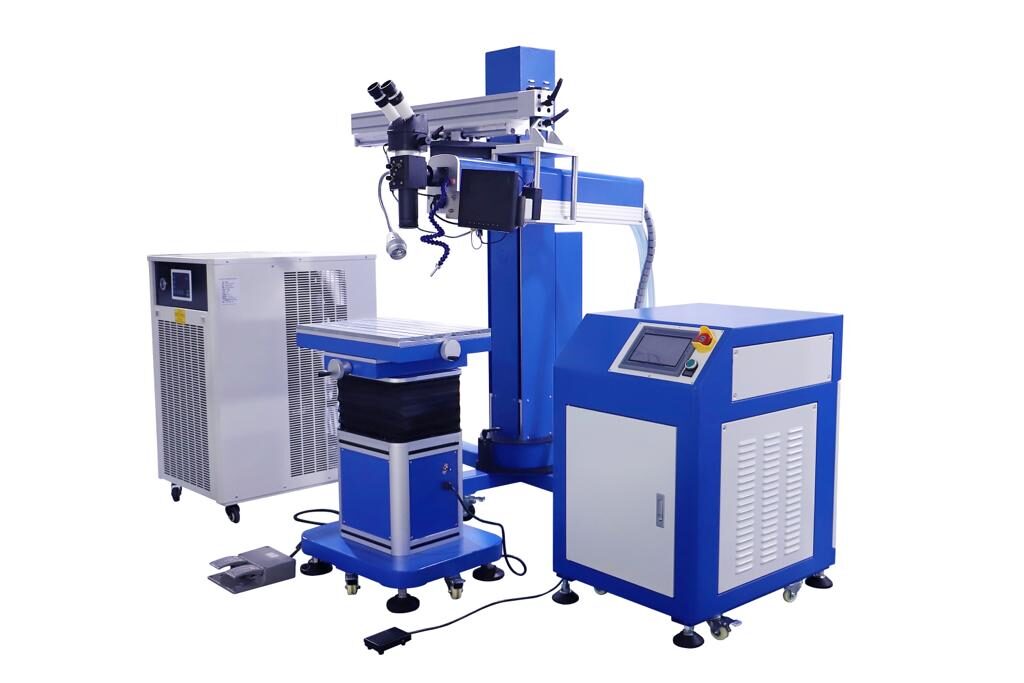
In general, the Mould Welding Machine for mould repair is represented by a fusion welding process, where the association of the parts takes place through the heat generated by the laser beam, this process results in the minimization of the risks of degradation of the part, ensuring an extremely efficient service.
- The main advantage of using the Mould Welding Machine for mould repair is that the laser generates low heat in the welded area due to its concentrated heat point, minimizing the risk of deformities in other areas of the part. This high precision also offers another advantage, which is the ease of welding in hard-to-reach spots, especially when dealing with thin or small, small, polished or textured parts.
- It is designed specifically for the mold industry, German technology and adopts unique frame design, suitable for all kinds of large, medium and small mold repair.
- It has ceramic light-gathering cavity, anticorrosion, heat resistance, chamber (8-10 years life), more than 8 million times the life of xenon lamp
- Laser head can rotate 360 degrees. The path is clear, electric lift up and down, driving back and forth, especially suitable for all kinds of big, medium and small mould repair.
- Using the world’s most advanced automatic shading system, it eliminates eye stimulation at work.
- Parameter setting adopts intelligent remote control, simple and fast operation.
- The 3D workbench can have electric crane.